CombiSys machine
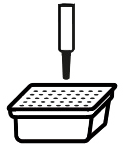
Machine type FVC 50606
The machine concept of this CombiSys filling and closing machine offers a high degree of flexibility. The grippers used for transporting the containers offer a greater working range without changing size parts. Dosing and closing are performed automatically with very high precision, sensitivity and 100 % IPC. To increase your production capacity, you can equip this machine with up to three dosing systems.
For more information about the CombiSys system solution, please click here
For more information about the CombiSys system solution, please click here
HIGHLIGHTS
- Modular design with standardized components
- 100 % IPC at full output
- Suitable for use in a RABS / in an isolator
- High process reliability
Type of machine | Output | Processing range |
---|---|---|
FVC50606 |
|
|
Easy and centralized operation
Compact design
Short set-up time
Optimal laminar air flow
Low-particle closure feed
Pharmaceutical design
Free-standing, calibrated load cells
ADVANCEDfill ensures that optimal use is made of your product batch.
ADVANCEDfill is a highly effective solution for processing your product. All containers in a batch are filled to the optimal level so that, at most, only the last container may need to be rejected. The ADVANCEDfill dosing system is equipped with a freely positionable needle holder. Product is dispensed directly into containers on the scales during start-up and running empty. This allows dose quantity to be monitored and setpoint deviations to be corrected in situ.
Benefits of the ADVANCEDfill dosing system:
- No need for manual intervention in the dosing area, e.g. during start-up or running empty
- Optimal product utilization
- Availability from batch sizes as small as 1
- Resource-friendly technology
CIP/SIP
"Cleaning in place – sterilizing in place" is a system for cleaning and/or sterilizing product-carrying parts as installed. Our CIP/SIP system offers a high level of process reliability while saving work and time, as well as cutting cleaning and sterilization costs.All parts which come into contact with the product are rinsed intensively with suitable cleaning media. There is no need to remove any parts. Once the cleaning and sterilization process has been completed, the entire system is cooled and kept under vacuum until the start of production. All applicable technical and pharmaceutical regulations, such as DIN, GMP and FDA, are observed and applied.
Barrier systems – RABS
Aseptic ambient conditions free of contamination can be created using RABS (Restricted Access Barrier Systems).
- Passive RABS
- Active RABS
- Closed RABS
- Isolator
Taking the building and room situation into account, these systems provide optimum air flow conditions.
Zero Reject
The Zero Reject Principle is a concept centered around technical features with a clearly defined goal: maximizing efficiency for our customers. The aim is to avoid product loss, be it due to overfilling or underfilling, missing closures or difficulties with the supply of product supply to the individual dosing positions. To mitigate these and other potential factors that could negatively impact efficiency and output, we offer the following solutions as part of our standard portfolio:- 100 % IPC bei voller Leistung
- Re-stoppering
- Refilling on the weighing cell
- Re-capping
- Crimp-Cap-Inspektion